Image may be NSFW.
Clik here to view.
Clik here to view.
Clik here to view.
Clik here to view.
Clik here to view.
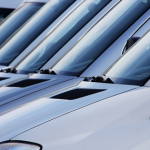
Equipment is expensive and so is repairing it. Get more life and out of your rolling assets and require fewer repairs with integrated asset tracking and telematics systems.
In the Telematics Update article, “Fleet telematics—Managing fleets in difficult economic time,” Mark Forrest, managing director of Trimble’s Field Service Management (FSM) division, comments on the importance of efficient management and utilization of vehicle fleets: “the capabilities of modern field service management solutions can improve a company’s productivity and level of service by enabling every aspect of a mobile operation to be identified, measured, and analyzed.” When companies understand what’s going on with their equipment, they can use it smarter and more efficiently in order to save costs and extend the life of the equipment. Follow these best practices to get the most longevity and functionality out of every asset in your fleet.1. Use telematics to track asset performance
Companies with telematics tracking capabilities have instant visibility into their rolling assets so they can monitor equipment performance and functionality. According to Vehicle Service Pros: “these [telematics] technologies use intuitive dashboards to monitor temperatures, door openings and fuel levels, change set points and other control parameters, modify operating modes and respond to alarms using any computer, tablet or smartphone connected to their secure network.” With this additional information and insight into their equipment, companies know exactly when something needs repaired, how to care for the equipment, which workers might be using the equipment recklessly, and how to remedy problems.2. Establish automated alerts based on telematics data
The performance information companies gain from telematics systems allow them to take their vehicle diagnostics solutions to the next level since they provide real-time data drawn directly from the equipment. Now, instead of guess-work, companies can improve vehicle maintenance and service scheduling by triggering alerts about engine difficulties before they become a major problem.3. Schedule preventive maintenance visits to inspect equipment
Asset tracking and telematics systems can work in unison with preventive maintenance scheduling to ensure that each fleet asset receives regularly scheduled maintenance. Like alerts, preventive maintenance visits can be scheduled as needed based on equipment performance, or in regularly scheduled intervals to maintain and measure equipment performance so companies can maximize rolling asset functionality and get more life out of their equipment.4. Analyze telematics data
Having large amounts data doesn’t matter much if companies don’t have a way to store and make sense of it. By connecting the telematics data to stakeholder web portals, organizations can create web pages with customizable widgets that raise key stakeholder visibility to important data and manage future fleet activity to key performance indicators.The Effects of Using Technology to Care for Your Equipment
Efficient management and utilization of rolling assets can have a major impact on a company’s annual spend, which is why it’s so important for organizations to make use of technology to extend the life of their equipment. Modern field service management and telematics solutions improve companies’ productivity and service levels by identifying, measuring, analyzing, and planning ways to make equipment work more efficiently and last longer with fewer repairs.Field Guide to Service Process Automation
Tired of performing time-consuming manual tasks and running disconnected service operations to keep your assets running smoothly? Automate alerts in your organization to manage assets and extend the life of your equipment.
Image may be NSFW.Clik here to view.

Like this post? Subscribe to our Field Service Management Blog for original weekly content updates.
Image may be NSFW.Clik here to view.
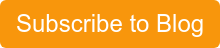
The post 4 Best Practices to Extend Your Equipment’s Lifespan with Asset Tracking and Telematics appeared first on MSI Data.
Image may be NSFW.Clik here to view.
